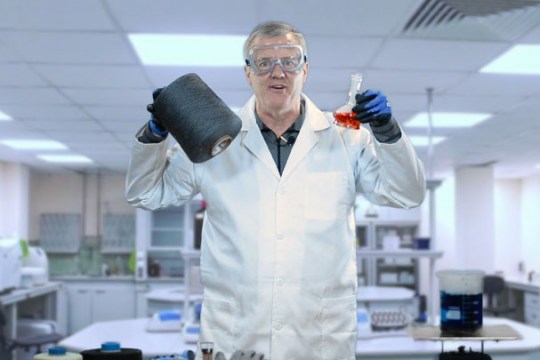
What Makes a Glove Cut-Resistant?
Cut-resistant gloves and sleeves are an essential part of most safety programs. But how do you choose the right gloves for extreme cut hazards and how exactly does a knit glove protect your workers from cuts and lacerations? The answer? It’s all in the yarn!

Traditional Cut-Resistant Gloves
Traditional gloves and sleeves are made with yarn constructed with an inner core bound by an outer wrap. The outer wrap is typically made of cut-resistant material (HPPE or Aramid) with some added filler like nylon, polyester or spandex to make the material flexible. The core, which gives traditional machine knit gloves their higher cut levels, can be made from any of several different materials or even a few materials combined:

Fiberglass
Fiberglass provides the lowest cut resistance – generally from A2 to about A4.



Steel
Steel provides higher cut resistance than fiberglass, but is the heaviest core material and also the most stiff and rigid.



Basalt
Basalt offers cut protection as high as A4. These fibers offer low moisture absorption and high thermal resistance.



Blended Core
Any of these three materials can be blended together in different combinations, and while that can increase the cut-resistance, it can also result in a heavier glove.


New Advancements in Yarn Materials and Construction
While these were the only choices for many years, new materials, technologies, and methods of yarn construction now give you more options than ever before!

Lightweight Cut-Resistant Gloves
New innovative shell materials allow manufacturers to create cut protection that’s 50% lighter than comparable gloves with the same cut protection. These gloves are made just like traditional cut-resistant gloves, but the strong and light core within the yarn creates a glove material that resists cuts without the weight.
That means gloves fit like a second skin so workers can use them to pick up and assemble even very small parts. The material’s breathability and its natural flexibility combine to make a cool, comfortable glove that workers have almost no reason to take off.


Extreme Cut-Resistant Gloves
Industries like metal or glass fabrication, auto manufacturing, and many others require cut protection that exceeds what traditional gloves can comfortably give them. While there’s always the option to add steel wire into the knit of a glove, that makes the overall product stiffer and less comfortable. New core materials and yarn-wrapping methods now make flexible, comfortable gloves with cut-resistant ratings as high as A9.


Coreless Cut-Resistant Gloves
While all of these innovations are great news for most workers, there is a small subset of people who need something different. That’s because when gloves and sleeves begin to wear, core materials can break, allowing microscopic pieces to poke through the fabric. Workers who are prone to contact dermatitis can experience redness, rash, itching, and pain. New coreless yarns eliminate this irritation by removing the core.
These yarns get their cut-resistance by infusing fibers with strength-enhancing micro particles. The resulting materials produce a comfortable cut-resistant glove that’s 20% lighter than a traditional HPPE of the same cut level that’s actually cool to the touch to keep the wearer comfortable while working – without irritation or discomfort.
How to Choose the Right Cut-Resistant Glove
It’s always a good idea to wear-test any gloves you’re considering so you can be sure that they’re the best glove for your application and environment. Cost is always an additional factor, but testing samples will let you determine if a more expensive glove will last substantially longer than a cheaper alternative. And while all of these new choices might mean you have a few more to test, the good news is you can probably find the perfect glove to keep your people safe, comfortable, and compliant!
Take a look at some of the newest glove innovations in: