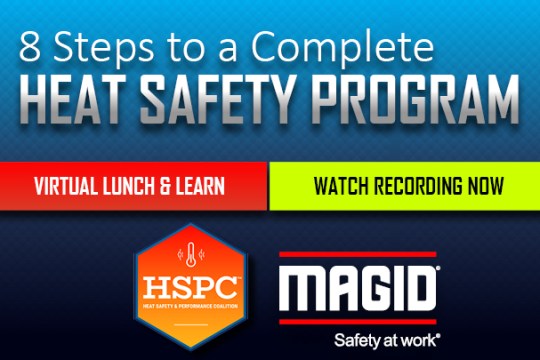
8 Steps to a Complete Heat Safety Program Toolkit
Safety Training
See All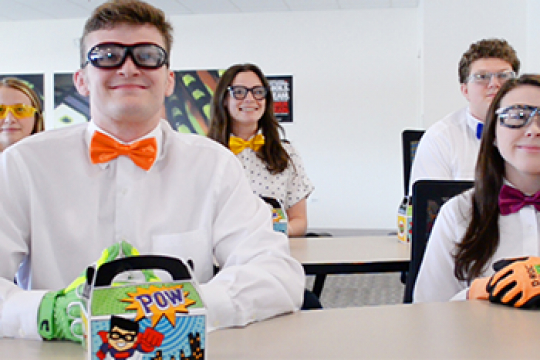
4 Tips for Safety Orientation & Beyond
Training is important for everyone. But we all know the newbies are the ones who need it most.


Why Do New Workers Get Hurt More?
Obviously, a worker with years of experience is going to be more proficient than someone who just started in their trade. But learning on the job can be riskier than you might think.
Lack of Experience
The Institute for Work & Health in Toronto reported that “workers who had been in a job a month or less had three times the risk of a lost-time injury as those who had been in a job for over a year.” And later analysis found that this higher level of risk continues through a worker’s entire first year.
High Risk Tolerance
Another big factor is lack of experience in understanding and evaluating risk. Lack of experience in their current job and perhaps in general may cause new employees to underestimate the consequences or likelihood of an accident and take unnecessary risks.


How to Protect New Workers
These facts may not be surprising to seasoned safety professionals, but they do suggest that we might need to train our newer workers differently – giving them more reinforcement and follow-up even after they complete their required safety orientation training.

4 Tips to Help New Workers Stay Safe
Tip 1: Recognize Safe Practices!
Positive feedback is just as important as correction. As you walk your facility or job site, be sure to take a few extra minutes to observe the newbies doing their jobs. Give them a small reward, even if it’s just a “nice job!” when you see them following safety rules. Knowing they’re doing something right boosts their job confidence and reinforces good safety habits.
Tip 2: Have a formal check-in 30 days after they start.
New workers tend to pick up bad habits from others. They may have learned in training that they always need safety eyewear in the plant, but if they see their coworkers pushing safety glasses up for certain tasks, or forgoing them entirely, they’re more likely to do the same. Review the rules with them after a month on the job to prevent normalization of deviance.
Tip 3: Require in-house competency testing and schedule announced observances.
Before you let your newbies start working unsupervised, make them show you the right ways to follow their safety rules. In-house competency testing may be required by OSHA for certain jobs, but it’s a good idea to make it the rule for any safety protocol. Even when a worker demonstrates post-training competency, it’s important to schedule announced observances as they go through their first year and beyond. Watching them doing their job in what they believe is the safest way can give you crucial information about where they may need more training.
Tip 4: Follow up after a few months on the job.
New workers can be a valuable source of information to find any gaps you may have in your training program. Follow up at their 30-day check-in to ask what they’ve learned on the job and what they wish they’d been taught in their first weeks. Then add these lessons to new worker training to benefit the next group.
Keep your newbies injury-free on the job. Make sure they’re equipped, not just with the right gear, but with the right knowledge to stay safe!
Send safety reminders directly to your workers with fun safety training videos.
GIVE ME VIDEOS
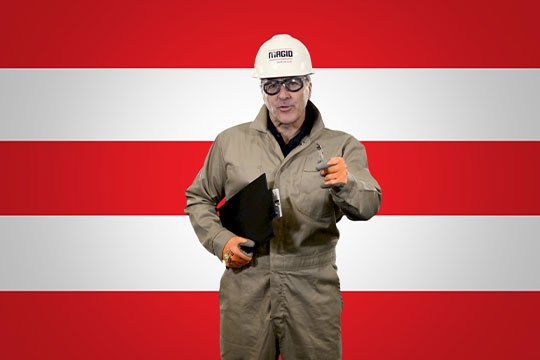
Making the Most of your Safety Reminders
Safety training isn’t a one-and-done event. It’s a dynamic and constant process of reminding workers about previous lessons and pointing out new hazards that may appear on the job. A network of safety reminders that use different methods of communication is the best way to keep safety on every worker’s mind.

Use these tips to reinforce your safety messages!
1. Conduct Both Announced and Unannounced Safety Inspections
Your everyday coaching is a good opportunity for spontaneous correction and praise. But it can be just as important to do announced observances as well. If your workers know that they’re about to be evaluated, they may review their safety rules and discover they haven’t been doing all they should, creating a valuable learning opportunity. Additionally, watching workers doing their job in what they believe is the safest way can give you crucial information about where they need more training.
2. Rotate Safety Reminders
Your workers may be aware of safety reminder posters you have posted around your workplace. But if they see them in the same location every day, your reminders will start to blend into the landscape over time. Make a schedule to rearrange posters once a month or even once a week to keep reminders visible and on your workers’ minds.
3. Bring in Outside Experts
Think about inviting a safety professional, physical therapist, or athletic trainer to talk to your workers. You can bring them in during training or toolbox talks to go over specific topics such as utilizing better ergonomics or showcasing the differences between different kinds of safety equipment. Sometimes a special event with an unfamiliar face can make lessons more memorable.
4. Have your Workers Enforce Safety Reminders
If your workers are inspired to think constantly about their own safety as well as that of their teammates, they can serve as a second set of eyes and ears at your worksite for safety hazards. Encouraging everyone to make team safety their business helps your company maintain a vibrant and supportive safety culture even in your absence.
5. Empower and Reward your Workers
Use the power of empowerment to reward workers who keep themselves and their coworkers safe. Whether they’re reminding their teammates to be safe, actively mentoring new workers, or bringing safety hazards to your attention, you can recognize them for their efforts and reward them with perks like gift cards, vacation days, or better parking spots to create a precedent for positive reinforcement in the future.
Get FREE posters to work into your rotation!
TAKE ME THERE
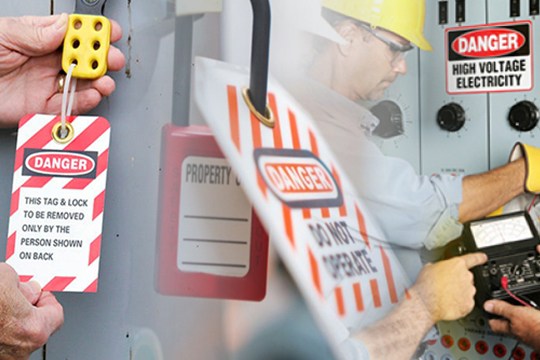
Lockout Tagout Training - 4 Steps to Safety
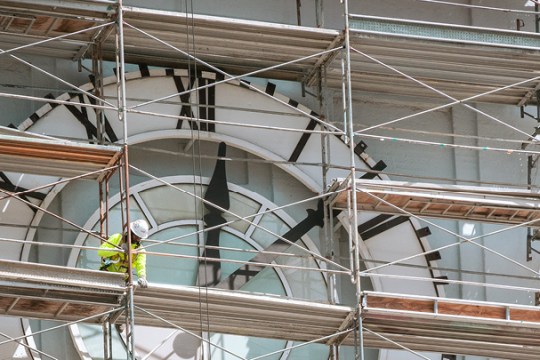
Train Workers to Maximize Scaffolding Safety
Safety Culture
See All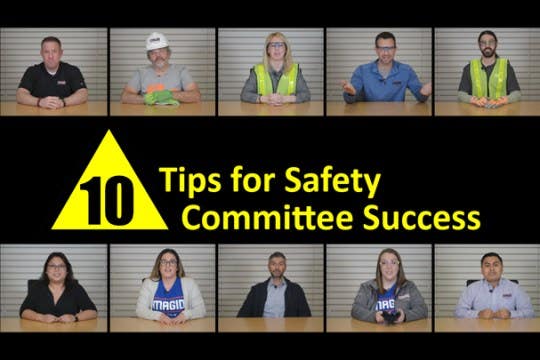
10 Safety Committee Ideas for Better Results
Most Safety Managers know that safety committees are a good idea, and many states actually require them by law. But is your committee doing all it can and should be doing? If you answered No, you’re not alone. A poll by Safety & Health Magazine found that only 32.6% of their readers said their safety committees were effective.
Here are our top 10 ideas to start improving today!
1. Review Your Safety Committee Mission Statement & Purpose
The purpose of a safety committee is to regularly bring employees from all levels of your organization together to improve, communicate, and promote workplace safety. Make sure everyone on your committee:
- Understands their role
- Understands the importance of what they’re doing
- Feels empowered to make recommendations for improvements
Take some time at your next meeting to review and clarify your safety mission and goals.
2. Include the Right People in Your Safety Committee Meeting
An effective safety committee should be a representation of your company, including a mix of:
- management
- salaried employees
- hourly employees
- stakeholders from different departments
Having a good mix of viewpoints can reveal different ideas and opinions and helps you anticipate any potential resistance. Including managers helps you to get decisionmakers on board and bought in early for any new ideas.
3. Make Time for Safety Committee Meetings
Don't squeeze committee meetings into your schedule. Carve out time for safety meetings and commit to them. Whether it's the first Monday of the month or the last Friday of the quarter, pick a day and stick to it so everyone knows it's a time that's important to your goals and mission!
4. Let Others Drive the Meeting
As a safety expert, you may find it difficult to take a back seat in your safety meetings. Though it may sound a little strange, it’s important not to be too active. Instead, serve as a coach or as a resource to the group so members feel free to speak up and be creative. Your role should be more about coordinating management and supporting employees.
5. Conduct a Group Safety Audit
Ask your safety committee to review your documented safety processes and procedures as a group to determine if there's a clearer way to communicate safety policies to front-line workers. If you don't have documented safety procedures, start creating them! Splitting up areas or processes to document might be a good way to get a new safety committee off the ground.
6. Have Your Safety Committee Walk the Plant or Jobsite
Ask your entire safety committee to walk the plant floor or jobsite and note safer, more efficient ways to get the job done including things like signage recommendations, PPE suggestions, and lighting improvements. Include outside experts to fill in gaps that might exist in your committee's expertise like an ergonomist or a professional safety assessor.
7. Give Your Safety Training a Trial Run
Use your safety committee as an audience to test your safety training materials and solicit suggestions. Periodic training reviews help keep your information timely and accurate. Check out additional sources of safety training classes and materials to keep your library fresh and up to date.
8. Look for Blended Safety Training Opportunities
As a group, brainstorm ways you might start to combine two or more forms of delivering information—for example, a combination of classroom instruction and an independent, self-paced online course. A University of Tennessee study showed that a blended learning program reduced both the time and the cost of training by more than 50%. The same study showed a 10% better result in learning outcomes compared with traditional training. You can even introduce fun safety training videos to help certain lessons stick.
9. Create a Safety Reward Program
Since you’ll have a mix of front-line workers and experienced managers in the same room, work together to create a rewards program that will motivate your employees and spark enthusiasm while helping to reduce injuries. Rewards can range from free PPE gear to paid days off to gift cards and even lottery tickets.
10. Keep Ideas Fresh
Once you've tapped the safety committee for their ideas and suggestions, consider rotating members. This opens your committee up for new viewpoints and experiences on an ongoing basis.
Remember to review this Top 10 periodically to avoid stagnation. Keeping ideas fresh is key to the kind of continued safety improvements that make your committee and your safety program effective now and for the long haul.
Download Safety Training Presentations to use in your next safety committee meeting!
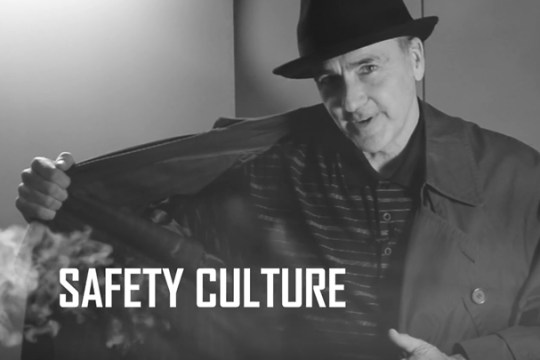
How to Get Your Workers Committed & Engaged for Safety
If your safety program only works when you’re in the room, your safety program isn’t working! So how do you get your team to follow the rules even when the boss isn’t around? Start by gauging your team's safety commitment level, then keep them engaged with these five tips:
- Make Your Safety Committee Inclusive
- Let Workers Help to Choose PPE
- Start a Reward Program
- Keep Communication Flowing
- Avoid a Culture of Blame

Gauge Your Team’s Safety Commitment Level
Start by figuring out where your safety culture is right now in terms of compliance. People tend to work at one of three levels:
Noncompliant
“I won’t do it”
Compliant
“I have to do it”
Committed & Engaged
“I want to do it”
It’s very common for workers to stay at Level 2 where they’re compliant only because they have to be. Why? Because many safety cultures rely on a system of catching people doing something wrong. So your people may only be vigilant until they think nobody is watching, making accidents much more likely.

Keeping Workers Committed to Your Safety Program
The secret to keeping your workers at Level 3 is to make everyone an active part of your safety culture through positive reinforcement and good leadership. Use these tips to keep your people engaged:
1. Make Your Safety Committee Inclusive
Be sure your safety committee includes people from all levels of your organization. You should have as many members in hard hats as you have in collared shirts to elevate workplace safety ideas and awareness. If workers feel heard, they’ll feel bought-in. And as a bonus, you’ll get their good input and ideas that are based on experience doing the job.
2. Let Workers Help to Choose PPE
Set up a PPE wear-testing program to allow your people to pick gear that they find comfortable and usable. Having a voice in the PPE they have to wear every day gives them ownership and makes them much more likely to willingly use it.
3. Start a Reward Program
Boost your safety culture with a safety incentive program. If workers know there are prizes for coming up with suggestions that make your facility safer, they’ll start actively looking for ways to improve. You might even give workers safety pop quizzes as you walk around your facility and provide simple but fun rewards like t-shirts or cool safety glasses for right answers.
4. Keep Communication Flowing
Help everyone contribute ideas and concerns by having smaller safety meetings, trainings, and toolbox talks. While some people are comfortable in large groups, you may be missing out on valuable input from the introverts on your team if you only ask for feedback when everyone is gathered. Smaller meetings of no more than 5 to 10 people can help workers feel more comfortable speaking up.
5. Avoid a Culture of Blame
Make sure your culture focuses on keeping everyone safer rather than punishing those who break the rules. Let your people know that coming forward with a safety concern won’t get someone in trouble, but it might save them from an injury or worse. Make it clear that it truly is their business if another worker is lifting a heavy item wrong or taking off their gloves by explaining the ripple effect that injuries can have on the whole team if something goes wrong.
Don’t hide in the shadows! Give your workers ownership and make everyone personally committed to safety.
CONTACT ONE OF OUR SAFETY SPECIALISTS TODAY!
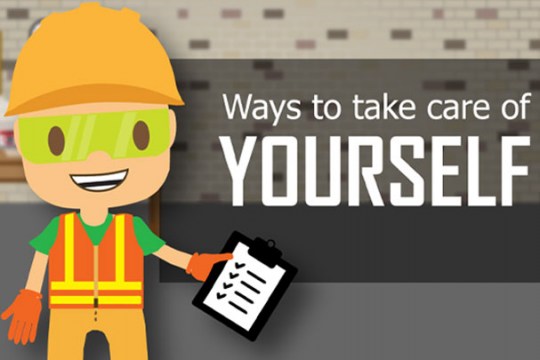
6 Ways to Reduce Work Stress for Safety Managers
It’s hard to build a safety culture when you’re tearing your hair out. Being responsible for the safety of your employees is a huge job in the best of times. Add in high turnover rates along with a looming recession and remaining supply chain issues and your stress level may be off the charts. Meanwhile, cuts and lacerations, arc-flash, slips, trips, and falls, and all the hazards you normally deal with are still part of the job. How can you keep your sanity with all you have to do? Try these six tips!

Stress Relievers to Make Your Job Easier
1. Plan Time to Plan
No matter what else is going on in the world, your company’s leaders expect production as usual and your customers are still looking to get their orders filled. That doesn’t mean you have to start putting out fires the moment you arrive for the day. Take ten minutes first thing in the morning to clear your head and organize and plan your schedule for the day or even for the week. Use digital calendars and planner apps to keep you organized and block out time when you need it. There’s nothing wrong with a planning meeting you schedule with yourself!
2. Reassess Your Routines and Schedules
Time is the biggest constraint for most safety managers. Carve out some time to audit your work schedules and daily routines to find inefficiencies. Although reworking larger operations can be a massive investment of time and energy, making smaller changes can be a fast and easy way to cut out redundant tasks and find opportunities to delegate.
3. Delegate Tasks to Your Employees
You can’t do it all yourself. Delegating tasks to some of your best employees will free up your time and give you more breathing room in your busy schedule. Your safety committee is a good place to find enthusiastic employees who want to make your workplace safer and perhaps even move up the ladder to take on more responsibility. Find your safety leaders and leverage them to reduce your own stress!

Stress Relievers for Safety Professional Wellness
4. Monitor your Stressors
Never forget that you’re just as human as your employees! Chronic stress can lead to symptoms like anxiety and high blood pressure as well as unhealthy coping habits like overeating. If you recognize situations that cause stress symptoms like headaches, stomachaches, anger, or frustration, take a moment to consciously note what set that stress in motion. Over time, you may be able to recognize these stressors when they occur so you can figure out how to change what’s causing them. For example, if you find yourself stressing every time you need to remind employees to wear their safety glasses, you can think about implementing new mentoring or training programs or even posting more safety reminders to take some of the pressure off of you.
5. Give Yourself a Break
When you feel the stress building, take a moment to step back and re-center your focus. Get up and stretch or walk around to get your blood flowing and switch your focus for a short while. Even closing your eyes and concentrating on your breathing for a few moments can slow your heartbeat and stabilize your blood pressure to help you think more clearly when you return to the task at hand.
6. Establish Boundaries
Establish boundaries to start or end your day on a controlled, focused note. Listen to music, your favorite sports radio, or a book on tape during your commute instead of thinking about work. After work, avoid checking your phone during dinner or family time so you can maintain a firm barrier between your work life and your home life, when possible.
Save yourself some time with our FREE,
ready-to-download safety training resources!
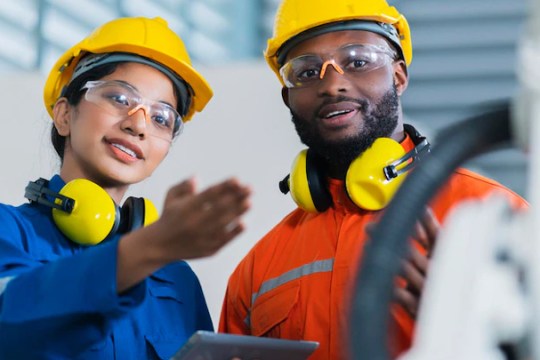
Safety Tips from Safety Managers
PPE: Choosing & Using
See All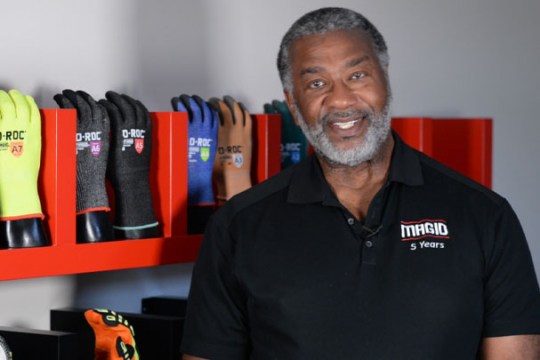
Incident Investigation After a Work Injury
When a worker gets a hand laceration, it’s only natural to think about going to a higher cut level glove. But that alone might not address the issue. You may need to look a little deeper into the safety incident to find the right solution.


Find the Correct Cause
It seems counterintuitive, but not all cuts are caused by a cut hazard. As you perform your workplace accident investigation, make sure you know the real cause of the injury. For example, sometimes a laceration actually starts as a puncture. The worker’s instinctive reaction is to jerk their hand away, which can cause a longer, cut-like injury. In this case, moving to a higher cut level alone might not prevent future incidents. Reviewing the application and the hazard as well as interviewing the injured worker will help reveal the true cause of the problem.


Understand the Hazard
The dangers in an application might not always be easy to see. While a thin, sharp piece of metal is an obvious cut hazard, even what looks like dull or heavy-gauge metal may have burrs that will penetrate gloves with lower puncture resistance. Be sure you’re taking every hazard into account when you review an application.


Test a Variety of Protective Work Gloves
If you’ve determined that you need to increase your cut or puncture resistance, remember that not all gloves are created equal. Gloves with identical cut- or puncture-resistant ratings can still vary slightly and may not protect equally. The only way to know for sure is to test them in your environment before you start trusting them to protect human hands.

Factors to Consider:
Protection Level
Choose the right level without going overboard. Work gloves for extreme hazards have become more comfortable in recent years than ever before. But since studies have shown that over 70% of injured workers were not wearing gloves at the time of injury, it’s still important not to overprotect in ways that might be less comfortable and decrease compliance. Higher protection doesn’t always have to mean the highest.
Glove Material
Consider both what the hazard involves (glass, steel, aluminum, etc.) and what, if anything, makes up the core of the yarn in your glove. Certain yarn cores may perform better than others with certain types of edges such as glass or stainless steel. Our internal testing found that gloves with stainless steel core yarns performed well against steel edges. But remember that edge testing is the best way to determine what glove is best suited for your application.
Testing on the Application and in the Environment
It can be difficult to accurately simulate your application and environment, so it’s generally best to test under real conditions. Here too, interviewing the injured worker about what exactly happened in an incident can give you good information for testing a replacement glove. One company we spoke to chose a glove for their application, but a worker was injured when catching a part that fell from a shelf. The part penetrated his glove under a force that wasn’t present in the normal application but was clearly possible in the job environment. Workers should be warned to avoid actions like this, but the possibility should be considered as a possible factor when selecting cut-resistant gloves.
Edge Testing
Since you obviously don’t want to test gloves by seeing whether your workers get injured in them, your best solution is having a safety expert perform edge testing. Edge testing is the process of using closed-cell foam or some other material to simulate a hand inside the glove. The tester then runs the filled glove over the hazardous item to see if the glove remains intact. Ideally, the tester will do this with more force than is expected in the application to be doubly-sure.

Above all, don’t go it alone! Particularly if you’ve had a workplace incident and investigation, it’s important to consult a safety expert who can guide you through testing in your environment and advise you on all your available options.
CONSULT A SAFETY EXPERT
Recommended Posts:
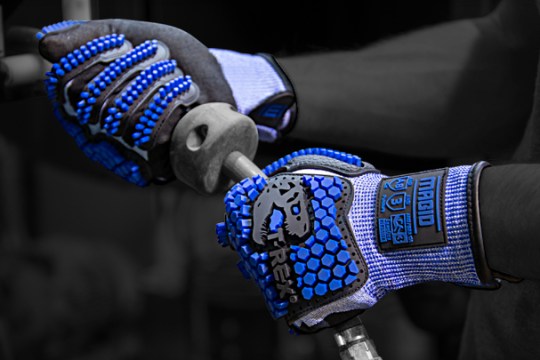
An Evolution in ANSI Level 3 Impact Gloves
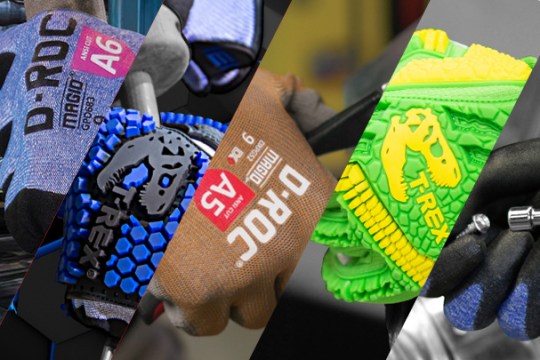
PPE: How to Get Your Money’s Worth
Calculate the Cost Benefit of New Technology
![]() VersaTek™ |
Magid’s VersaTek™ adaptive palm coating is a great example of a new technology in grip that has the added benefit of incredible durability. VersaTek’s coating is designed with special stabilizers that amplify your workers’ grip on objects that are wet, dry, oily, or rough. In addition to this intelligent grip that can adapt to different tasks and work environments, VersaTek also surpassed 30,000 revolutions in abrasion testing — greatly exceeding the baseline to achieve a Level 6 abrasion resistance rating. |
Top-of-The-Line Glove | Economy Glove | |
---|---|---|
Cost (per pair) | $7.75 | $2.61 |
Wear Time (in hours) | 63.87 (~1.6 pairs in a 40-hour work week) | 4.1 (~10 pairs in a 40-hour work week) |
Cost (per hour) | $0.12 | $0.64 |
Annual Cost | $2,487 | $13,050 |
Boost Your Environmental Sustainability
Make More Efficient Work Glove Choices
Here too, new technologies like VersaTek™ - with special stabilizers to enhance performance keep multi-environment workers at maximum efficiency and safety because they can assemble small parts, pick up oily and slick items, and handle rough and heavy materials easily in the same glove. No need for your workers to change their gloves to fit the task!
Add it Up: Comfort + Compliance = Safer Workers
![]() AeroDex® Gloves |
Magid’s innovative AeroDex® technology keeps worker comfort in mind while meeting the highest ANSI cut protection standards. AeroDex gloves are over 50% lighter than similar gloves with equal cut protection and are available up to ANSI Cut Level A9. Along with this noticeable lightness in weight, AeroDex shells are breathable and can make your employees’ skin feel cooler as they wear them. |
![]() DX+ Technology Gloves |
Similarly, Magid’s lightweight, coreless, cut-resistant DX+ Technology is 30% lighter than similar HPPE, doesn’t irritate your workers’ skin, and feels cool to the touch — all while providing cut-resistance up to ANSI Cut Level A6. Coreless technology means the glove yarn has been infused with strength-enhancing microparticles, which achieve higher cut-resistance levels without becoming uncomfortable or irritating to wear. |
![]() T-REX® Windstorm Gloves |
Cut-resistant shells aren’t the only glove category that has been redesigned with comfortable innovations. Magid’s T-REX® Windstorm Series® impact gloves are designed with an integrated CoolMesh® venting system that enhances airflow up to 60% and helps dissipate heat. These gloves also have Magid's M-Flex Defense System®, which is designed with 130 integrated flex points so workers can flex their hands comfortably. |
![]() M-Power Defense System™ |
New impact gloves feature Magid’s M-Power Defense System™, which is designed in a honeycomb pattern for thicker deflection points as well as space in-between for dexterity. This design, rated for Level 3 Impact Protection, also has an integrated ventilation system for up to nine times more airflow to keep hands cooler, drier, and comfortable. |
Analyze Your PPE Usage (With an Expert or By Yourself)
|
GET YOUR MONEY’S WORTH WITH THE LATEST INNOVATIONS!
SHOW ME INNOVATIONS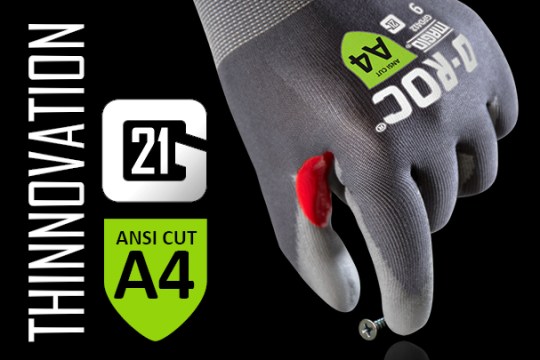
21-Gauge Work Gloves Just Got Even Better
Safety Managers' Secrets
See All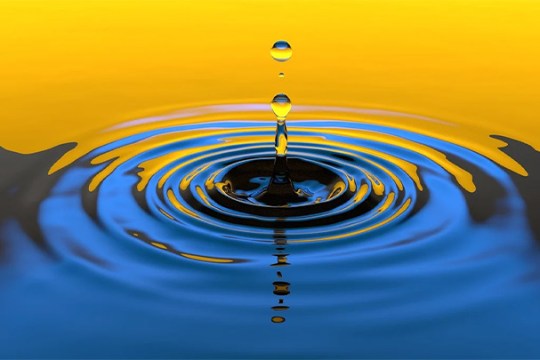
Emphasize The Ripple Effect
Shared By Ed, Safety Manager, Oil & Gas
When talking about safety, I make sure my people know, if you get injured, it’s not just you that suffers, it’s 120 families. An injury means an OSHA recordable. That means our OSHA Incident Rate goes up and that might mean we can’t have our company picnic or I can’t give promotions. So when you think about picking up that heavy box by yourself, think of everyone else!
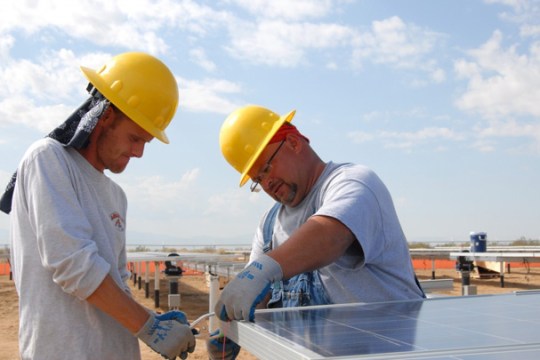
Assign New Workers A Mentor
Shared By Kevin, Safety Manager, Oil & Gas
We put our new hires through workshops, lectures, online training courses, and other traditional forms of training, but once they complete that, they are assigned a mentor from our safety team. The mentor is responsible for showing them how to apply the training that they just completed and guide them through their first project. By implementing this program we’ve eliminated 1.5 to 2 million dollars a year in unnecessary wait time for redoing work.
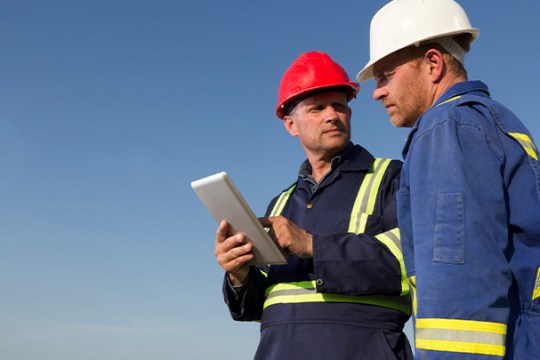
A Little Teasing Can Save a Worker's Hearing
Shared By Sean, Safety Manager, Manufacturing & IT
When I see people not wearing their hearing protection, I walk up to them and start “talking” but I don’t make any sound. It’s a friendly reminder of what they might experience if they damage their ears!
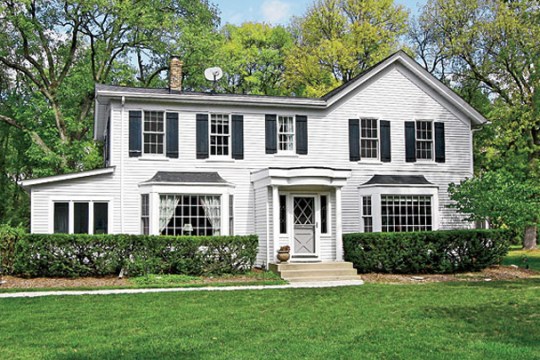
Take PPE Home
Shared By Jason, Safety Manager, Manufacturing & IT
We encourage our workers to take their PPE home with them so they can implement their safety training outside of work. We are proud to have so many employees who take safety seriously in all aspects of their lives. We had an employee who experienced a laceration incident at home. He was wearing his PPE when it happened and it saved him from what would have been a severed finger. While he has always known that the proper PPE is key to staying safe and in one piece, he says he’s a true believer now. That experience helped reinforce for him the importance of the proper safety equipment. After all, gloves are cheaper than stitches!